Leakage and corrosion in boiler air preheaters are closely linked. Both issues negatively affect boiler efficiency and safety.
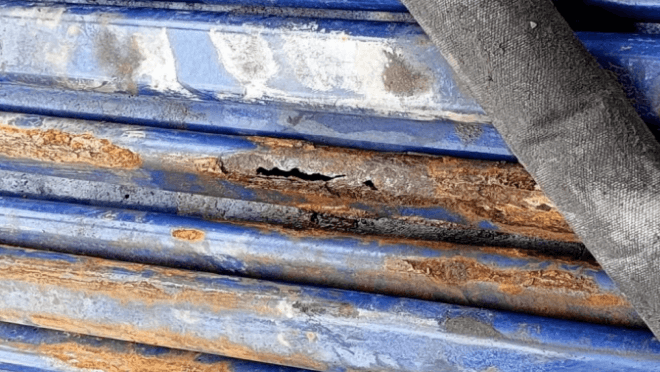
1. Impact of Leakage on Corrosion:
Worsening Corrosive Conditions:
When leakage happens, especially when air leaks from the positive pressure side to the negative pressure flue gas side, oxygen levels rise. This increase in oxygen accelerates metal corrosion in the air preheater.
Leakage can also cause uneven temperatures in the flue gas. Cooler spots can trigger dew point corrosion. This type of corrosion occurs when water vapor condenses into corrosive liquids at lower temperatures, which then attack the metal surfaces.
Increasing Ash Accumulation and Slag Formation:
Leakage often leads to more ash and slag inside the air preheater. These deposits lower heat exchange efficiency and create conditions that promote dew point corrosion, further damaging the metal.
2. Impact of Corrosion on Leakage
Damage to Sealing Structures:
Corrosion can harm the sealing structures of the air preheater, such as sealing plates and strips. These components are essential for proper operation and minimizing leakage. When corrosion occurs, the effectiveness of these seals decreases, leading to more leakage.
Effect on Heat Transfer Elements:
Corrosion also affects the heat transfer elements, like tubes and fins. It can cause the walls of these elements to thin, reduce their strength, and even create holes or cracks. These issues not only increase leakage but also lower the heat exchange efficiency of the air preheater.
3. Overall Impact
Efficiency Loss: Leakage and corrosion together lead to higher exhaust gas temperatures and lower boiler efficiency. Leakage increases the energy consumption of the draft fan and causes more heat loss. Meanwhile, corrosion reduces the air preheater’s ability to exchange heat effectively.
Higher Operational Costs: Regular inspections and maintenance of the air preheater are necessary to keep the boiler running smoothly. However, the damage and performance decline caused by leakage and corrosion significantly increase these costs.
Safety Risks: Severe leakage and corrosion can cause the air preheater to malfunction, potentially leading to accidents. For example, tube leaks may cause significant air infiltration, disrupting combustion. Similarly, intense low-temperature corrosion can lead to cracks in the preheater’s metal surfaces.
4. Solutions
Improve Sealing: Use advanced sealing techniques and materials to enhance the preheater’s sealing efficiency.
Enhance Corrosion Protection: Choose materials with high corrosion resistance for the air preheater. For example, the rare earth alloy heat pipe for air preheater launched by Bokk Tech, adopts sacrificial anode protection and has better anti-corrosion performance. Additionally, introduce additives to the flue gas to neutralize corrosive agents, and perform regular cleaning to remove ash and corrosion buildup.
Control Operating Conditions: Minimize corrosion and leakage by adjusting key operating parameters, such as the fuel’s sulfur content and exhaust temperature.
Routine Maintenance: Conduct regular inspections and maintenance to promptly identify and resolve any leakage or corrosion issues in the air preheater.
About Us
Shandong Bokk Tech is dedicated to solve the problem such as ash blockage, corrosion and excessive exhaust gas temperature in the tubular air preheater of small and medium-sized boilers. We primarily manufacture automatic cleaning devices for tubular air preheaters and corrosion-resistant heat pipes. Our products are widely used in the thermal power plants, chemical plants, new energy sector, etc.
We offer customized services to customers around the world, allowing us to adjust product dimensions and other specifications based on your specific needs, to improve air preheater heat efficiency.
Share The Post